
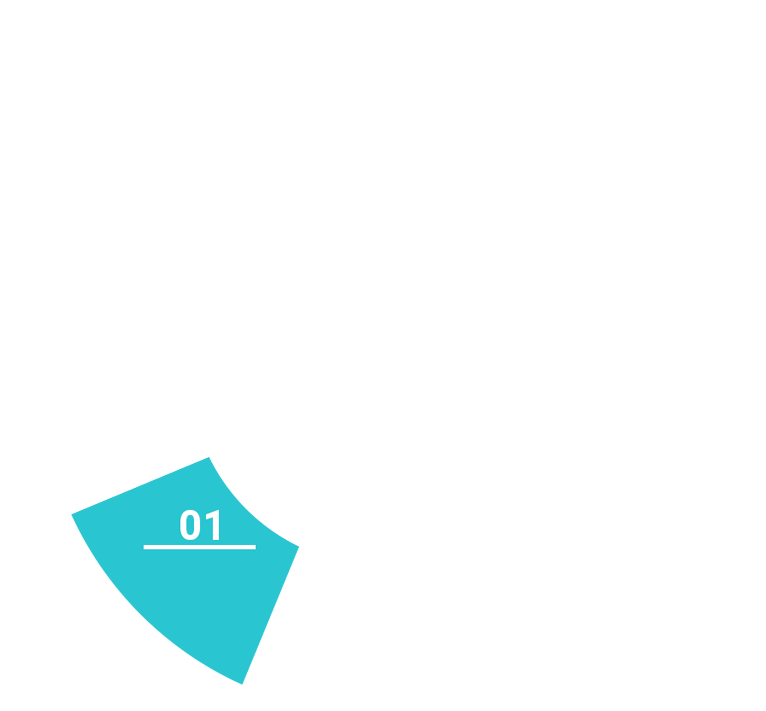
- Projektplan
- Analysegrenzen
- Basis FMEA
- Lessons Learned

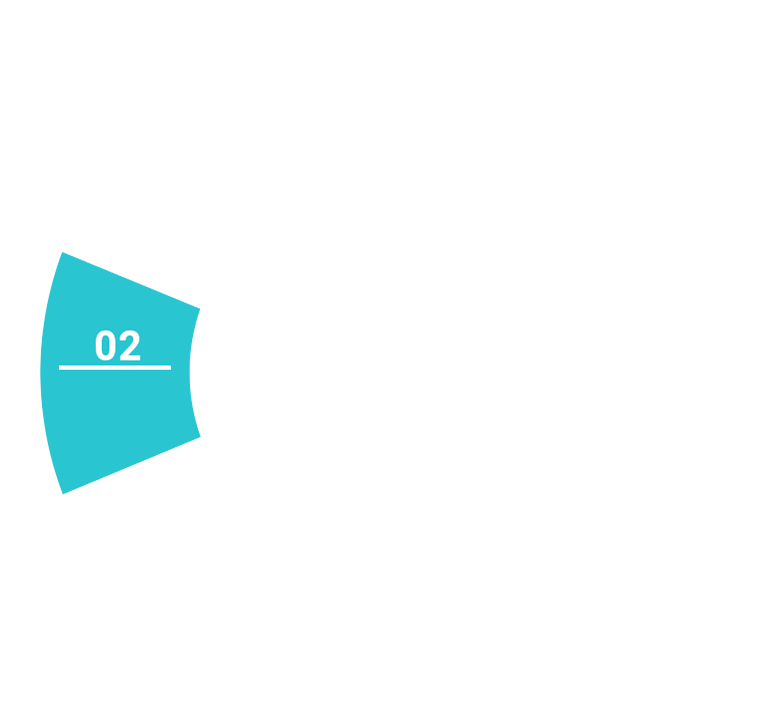
- Strukturbaum
- Block- / Boundary-Diagramm
- Prozessflussdiagramm
- Schnittstellen

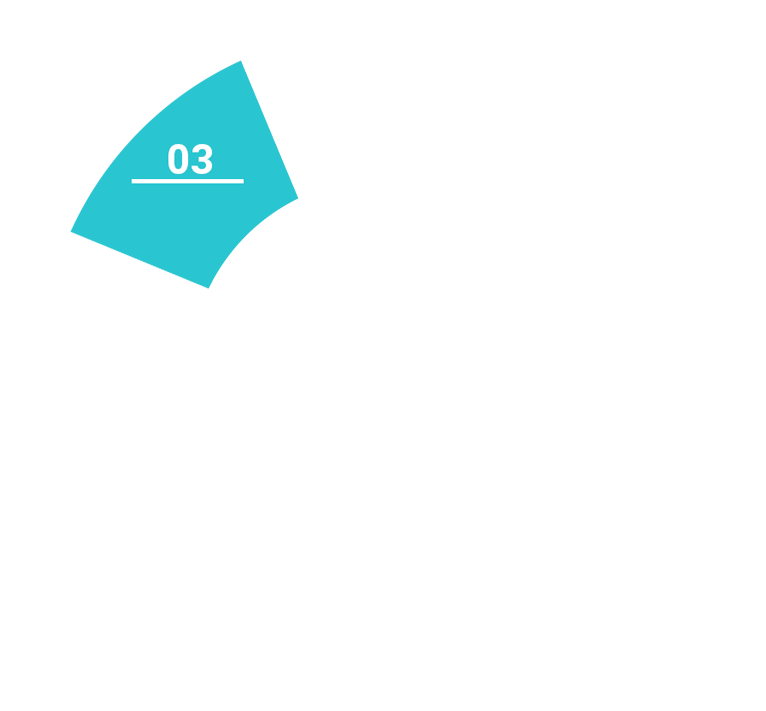
- Funktionsnetz
- Parameter-Diagramm
- Zuordnung von Anforderungen und Merkmalen

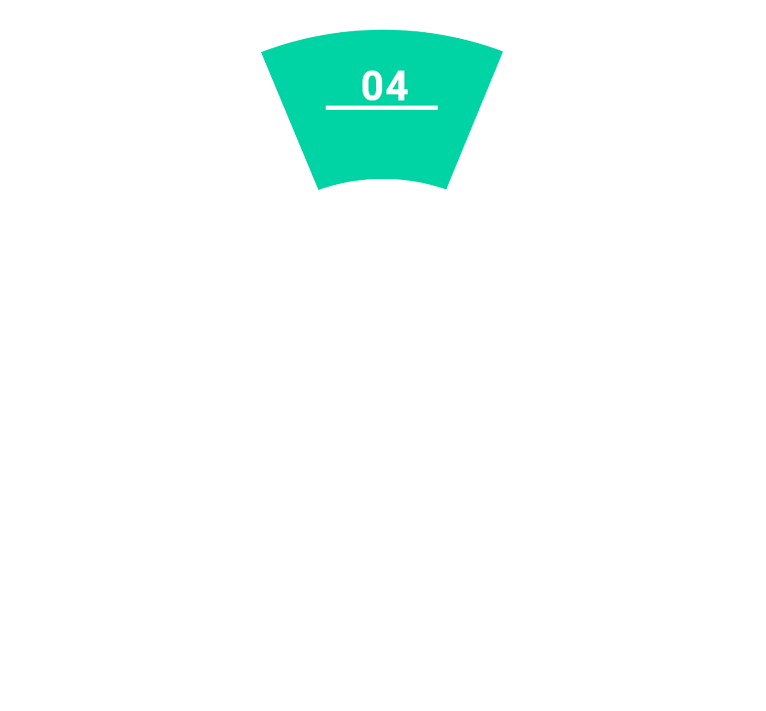
- Ableiten der Fehlfunktionen aus Funktionen
- Fehlernetz aus Ursache, Fehler, Folge

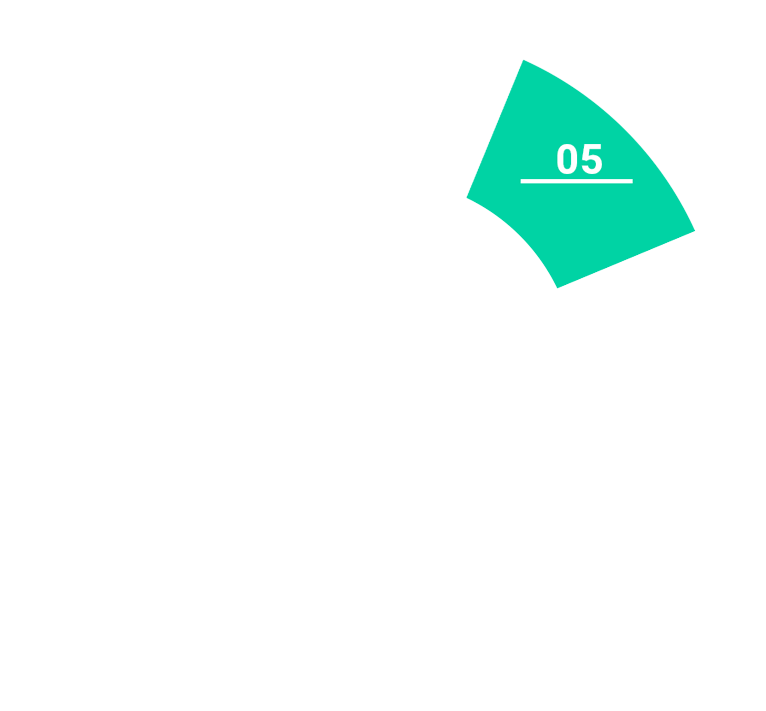
- Zuweisen von Fehlerursachen
- Bewerten von Bedeutung, Auftreten, Entdeckung
- Bestimmung der Aufgabenprioritäten

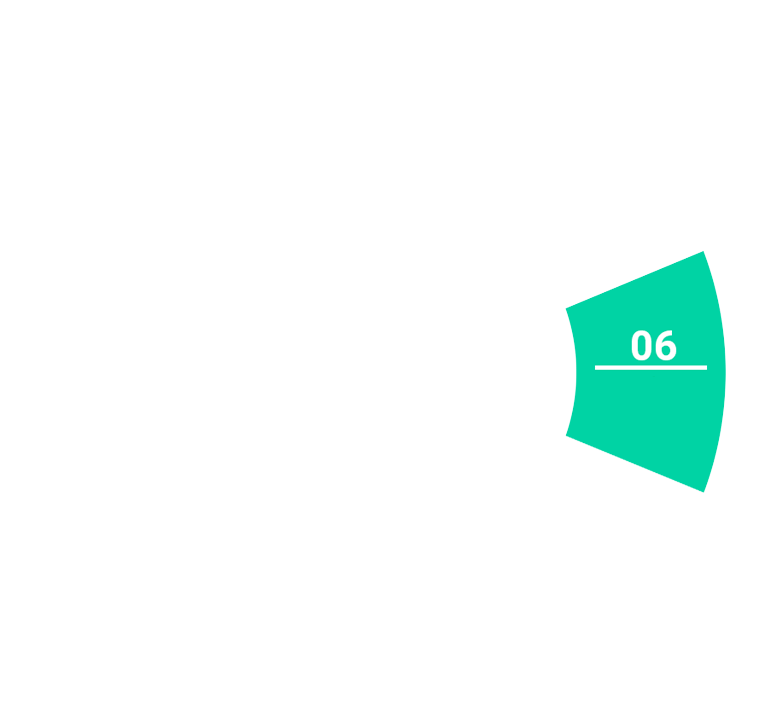
- Festlegung von Verantwortlichen und Terminen
- Bestätigung von Risikobewertungen auf der Basis von Nachweisen
- Dokumentation der Wirksamkeit

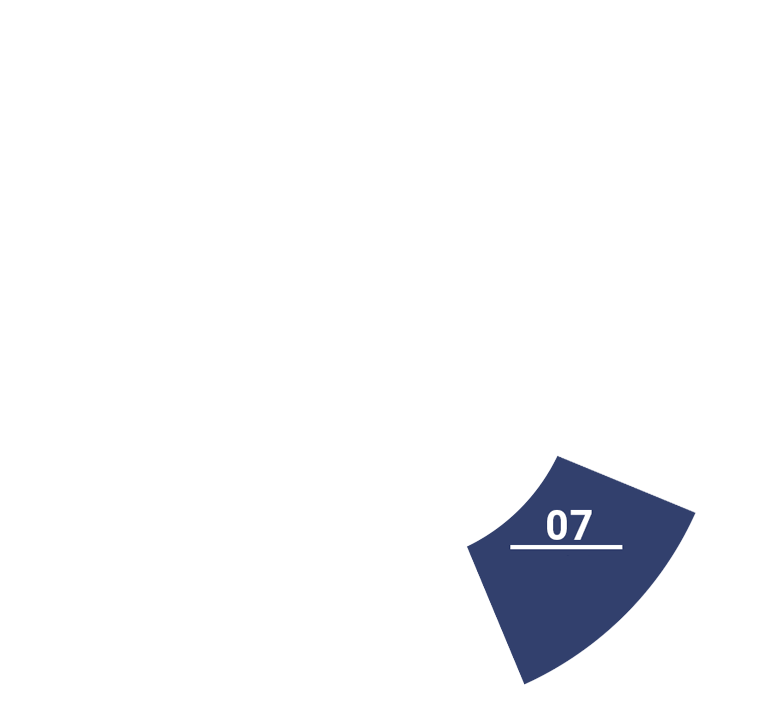
- Bestimmung der Aufgabenprioritäten
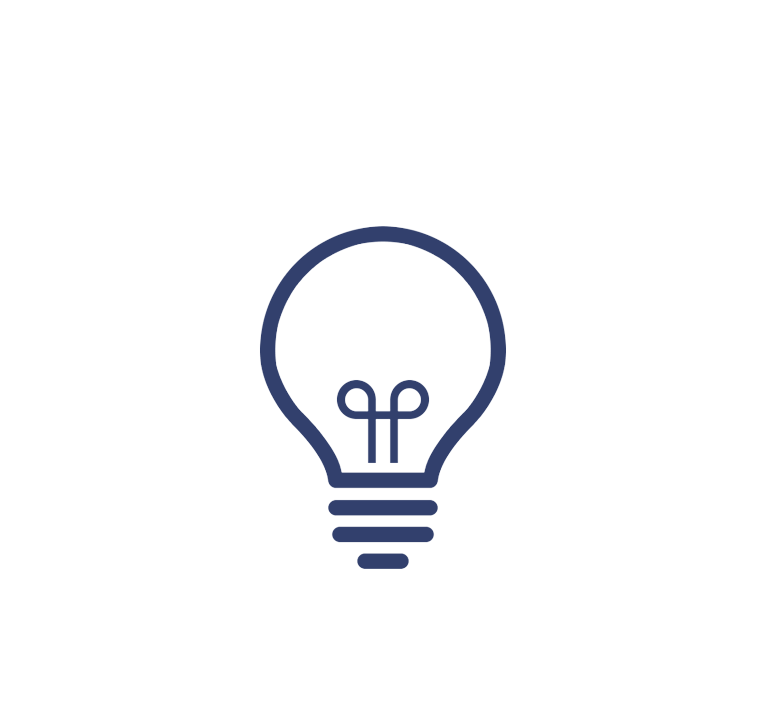

Die gemeinsame FMEA-Methodenbeschreibung von AIAG und VDA zur Entwicklung von FMEA in der Automobilindustrie wurde im August 2019 erstmalig und zeitgleich in englischer, deutscher und chinesischer Sprache veröffentlicht. Der Kern der Methode werden durch sieben Schritte abgebildet, welche hier im Detail und übersichtlich dargestellt sind. Sie gelten für jede Art von FMEA: System-FMEA, Design FMEA, Monitoring und Systemreaktion (MSR)- FMEA sowie Prozess-FMEA.
Die sieben Schritte der FMEA stellen einerseits den Leitfaden zur Entwicklung von FMEA dar. Anderseits bilden die sieben Schritte auch den Kern von FMEA-Ausbildungen, FMEA-Reifegradbewertungen sowie Kompetenz-Feststellungsverfahren für FMEA-Experten. Ergänzt werden die sieben Schritte der FMEA durch die Anwendung von Blockdiagrammen, insbesondere Boundary- und Parameter- Diagramme. All diese Werkzeuge und deren zielführenden Anwendung dienen dem gleichen Ziel: der Risikominimierung von Innovationen im Kontext von Design und Prozess, damit störungsfreie Serienanläufe gelingen. Die Website von Dietz Consultants verfolgt die Zielsetzung, dem Besucher umfassende und aktuelle Informationen zur FMEA-Methode zu geben.