
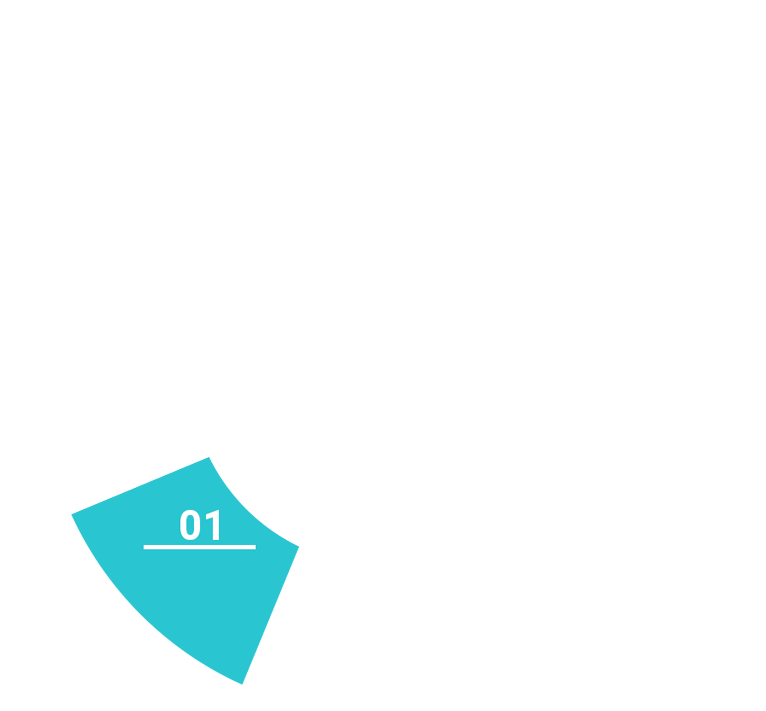
- Project plan
- Analysis limits
- Basic FMEA
- Lessons learned

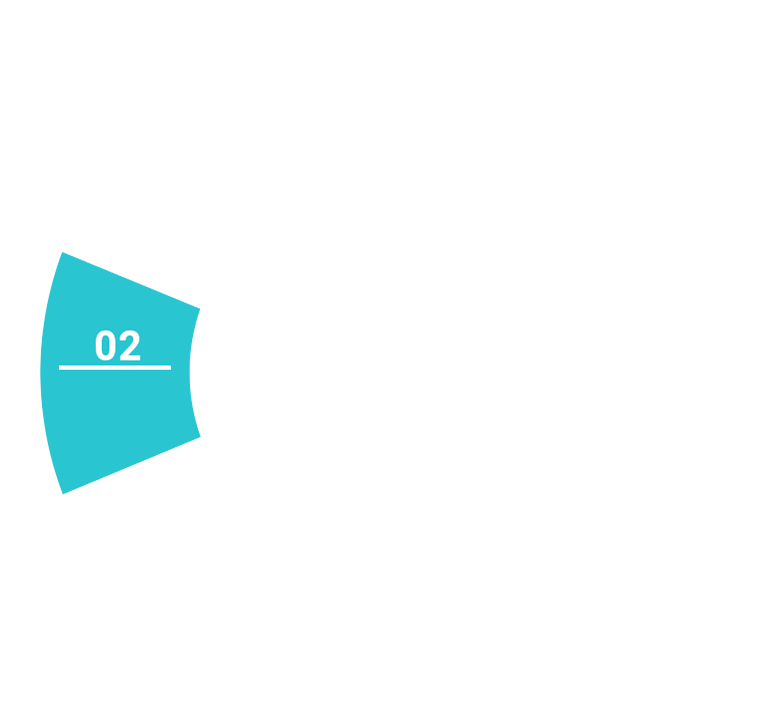
- Structural tree
- Block-/ boundary diagram
- Process flowchart
- Interfaces

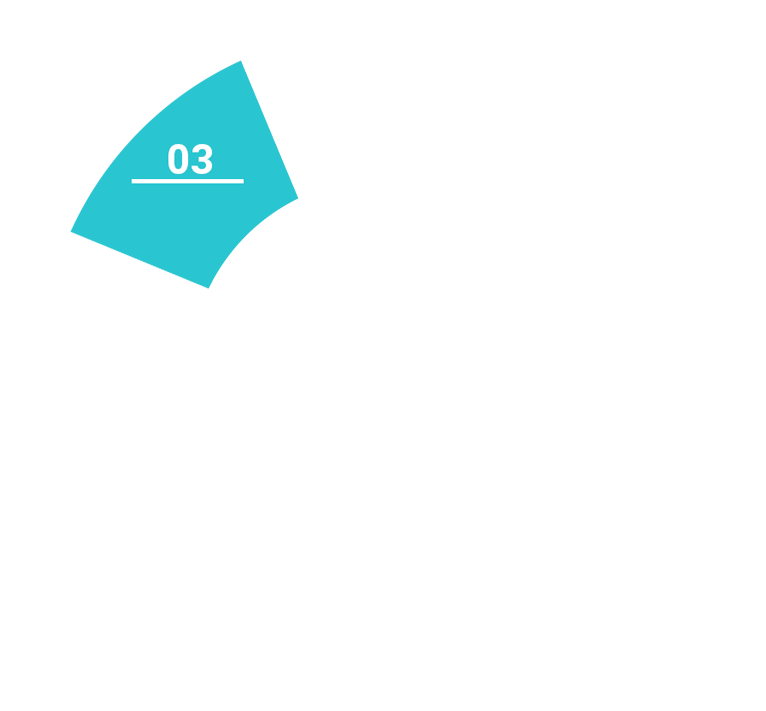
- Function net
- Parameter diagram
- Assignment of requirements and characteristics

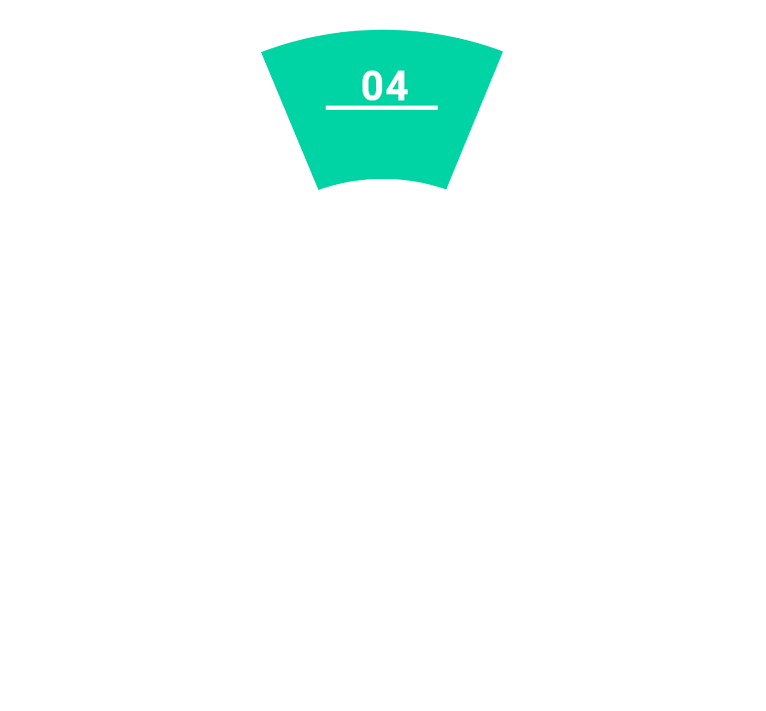
- Deriving the malfunctions from the functions
- Failure net listing cause, failure and effect

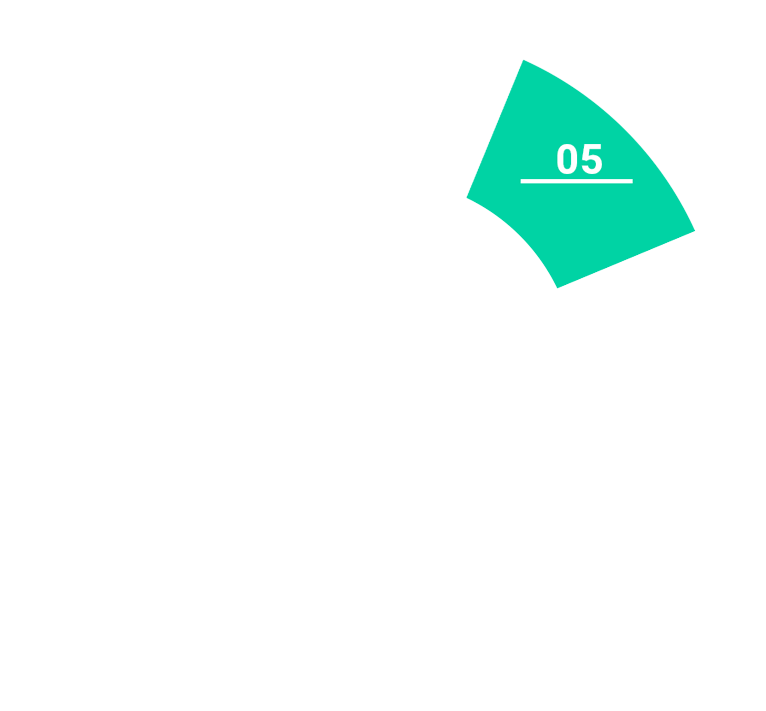
- Assigning failure causes
- Evaluating significance, occurrence and detection
- Determination of task priorities

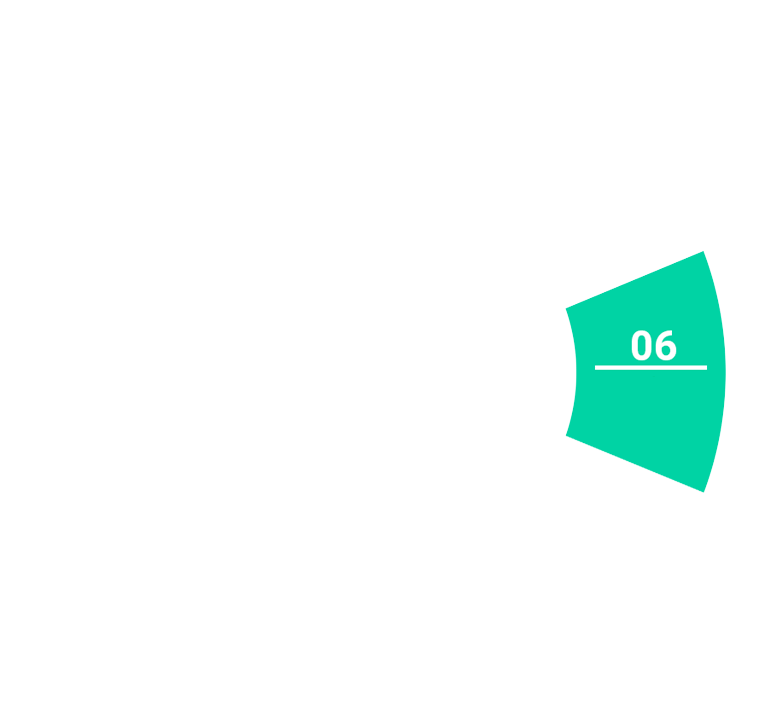
- Determination of responsible persons and deadlines
- Confirmation of risk assessments based on evidence
- Documentation of effectiveness

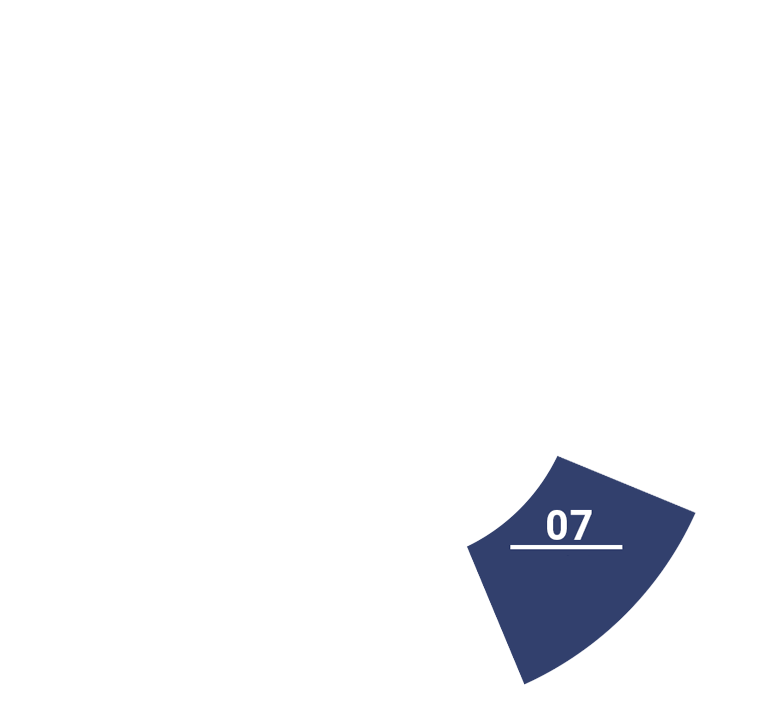
- Determination of task priorities
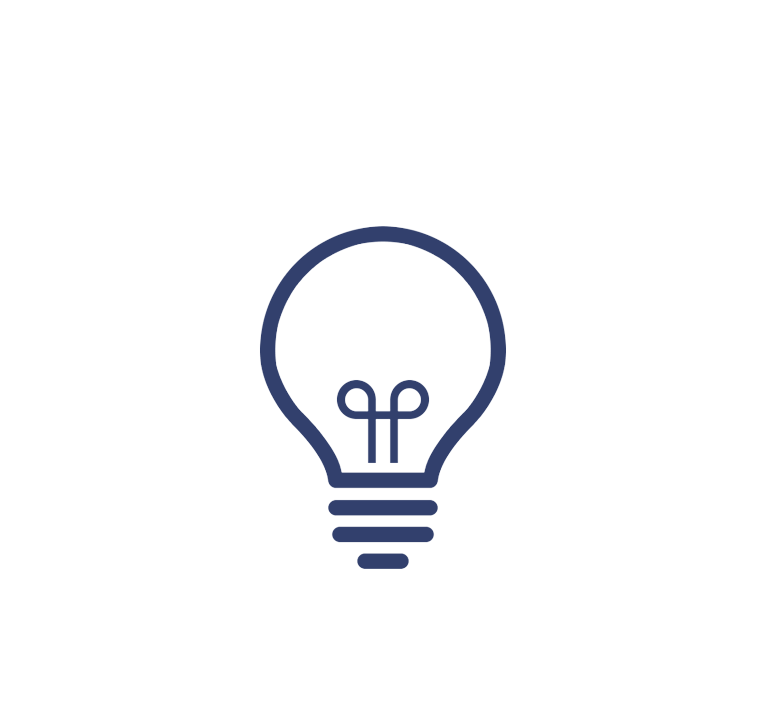

The joint AIAG/VDA FMEA method description for the development of FMEA in the automotive industry was published for the very first time – simultaneously in English, German, and Chinese – in August 2019. At the core of the method are seven steps, which are presented here clearly and in detail. They apply to all types of FMEA: system FMEA, design FMEA, monitoring and system response (MSR) FMEA, and process FMEA.
On the one hand, the seven steps of FMEA constitute the guidelines for the development of FMEA. On the other hand, the seven steps also form the basis for FMEA training, FMEA maturity evaluations, and competence assessment procedures for FMEA experts. The seven steps of FMEA are complemented by the use of block diagrams, in particular boundary and parameter diagrams. All these tools and their targeted application serve the same goal: to minimize the risk of innovation in the context of design and process, and thereby to ensure trouble-free production start-ups. The Dietz Consultants website aims to give visitors comprehensive, up-to-date information on the FMEA method.